Defect Analysis and Applications
In some systems, the constant interaction of a trained operator is required to determine whether the status is acceptable or rejectable. More sophisticated systems use automatic defect recognition (ADR) or artificial intelligence software that determines the status, without the constant need for an operator. Complexity depends on the use of the system, which might determine part presence or absence, placement, position, density variations, or size variations. For example, in certain instances, defective conditions are known and ADR algorithms, or step-by-step procedures for solving problems, are written. If the ground pin of an airbag initiator is being inspected for proper diameter and location, the ADR can be written to look where the ground pin should be. If it is not in the correct position, the ADR rejects it. This method allows for the examination of specific regions of interest (ROI), permitting faster inspection and decreasing the amount of image storage space.
More complex analysis may involve the program’s algorithm to determine whether, in a certain ROI, there are any deviations such as discontinuities, pores, cracks, or inclusions. The RTR system may be tasked with automatic inspection (without operator interaction), making various required checks and proper archival records all at a relatively high rate of speed. Figures 18 through 22 show some of the different objects that are inspected with RTR systems but almost any component could be inspected use RTR.
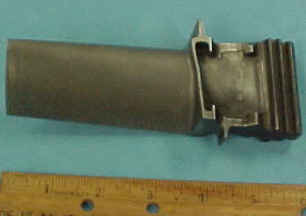
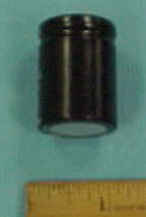
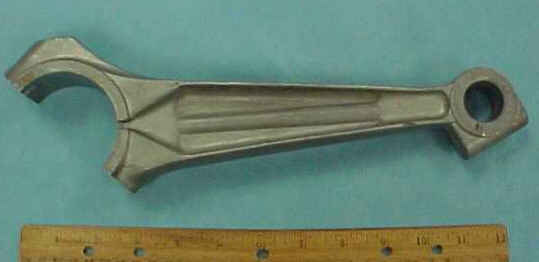
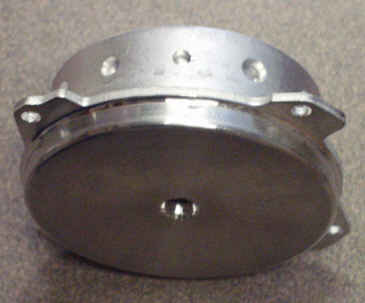
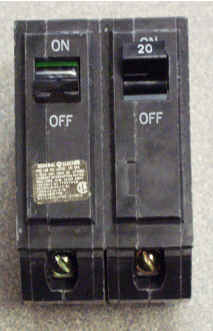